Maintenance Guide for the Cooler Core
Release time:
2024-04-29
Cooler plays a pivotal role in modern industrial production and daily life, and its stable operation is essential to ensure the safe and efficient operation of various mechanical equipment. As its core component, the maintenance of the cooler core is the most important. This article will introduce the maintenance methods and precautions of the cooler core in detail to help readers better understand and apply.
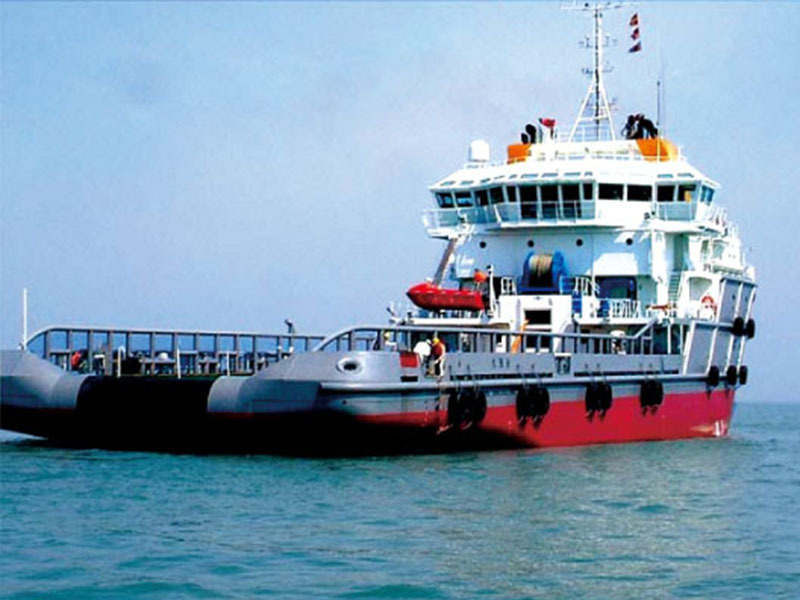
Maintenance Guide for the Cooler Core
1. Introduction
Cooler plays a pivotal role in modern industrial production and daily life, and its stable operation is essential to ensure the safe and efficient operation of various mechanical equipment. As its core component, the maintenance of the cooler core is the most important. This article will introduce the maintenance methods and precautions of the cooler core in detail to help readers better understand and apply.
The Importance of 2. Cooler Core
The main function of the cooler is to take away the heat generated by the equipment through heat exchange to ensure the normal operation of the equipment. The cooler core is the key component to achieve this function, and its performance directly affects the cooling effect and the safe operation of the equipment. Therefore, the maintenance of the cooler core is very important.
3. Maintenance Procedures and Precautions
1. Regular inspection
Regular inspection of the cooler core is the key to prevent failure. The inspection contents include but not limited to: whether the pipeline connection is loose, whether there is leakage, whether there is dirt on the surface of the core bladder, etc. If any abnormality is found, it shall be handled and recorded in time.
2. Cleaning and maintenance
Cleaning and maintenance is an important step in maintaining the performance of the cooler core. In the cleaning process, special cleaning agents should be used to avoid the use of corrosive chemicals. When cleaning, attention should be paid to remove the scale and impurities in the core bladder to ensure its good thermal conductivity.
3. Replace the coolant
The performance of the coolant directly affects the cooling effect and service life. Therefore, the coolant should be replaced regularly, and the appropriate coolant should be selected according to the operating conditions of the equipment. When replacing, the cooling system should be thoroughly cleaned to avoid mixing the old and new coolant.
4. Tightness check
The sealability of the cooler core has a crucial influence on its performance. If the sealing is not good, it will cause the coolant to leak, which will affect the cooling effect and equipment operation safety. Therefore, the tightness of the cooler core should be checked regularly, and if leakage is found, it should be handled in time.
5. Reasonable use
The rational use of the cooler is the key to extend its service life. Long-term overload operation should be avoided to avoid damage to the cooler core. At the same time, avoid running at too high or too low temperatures to ensure its normal operation.
4. Common Faults and Treatment Methods
1. Coolant leakage
Cause of failure: it may be caused by aging of seals, loose or damaged pipelines, etc.
Treatment method: check the seal and pipeline, if any damage should be replaced in time.
2. Decreased cooling effect
Cause of failure: It may be caused by coolant pollution, blockage of the core bladder or insufficient coolant.
Treatment method: check the quality of the coolant, clean the core tank, supplement the coolant, etc.
5. Summary
The maintenance of the cooler core is of great significance for ensuring the safe operation of the equipment and prolonging the service life. This paper introduces in detail the maintenance steps, precautions and common fault handling methods of the cooler core, hoping to be helpful to readers. In actual operation, a reasonable maintenance plan should be formulated according to the equipment conditions and operating environment, and strictly implemented to ensure the normal operation of the cooler.